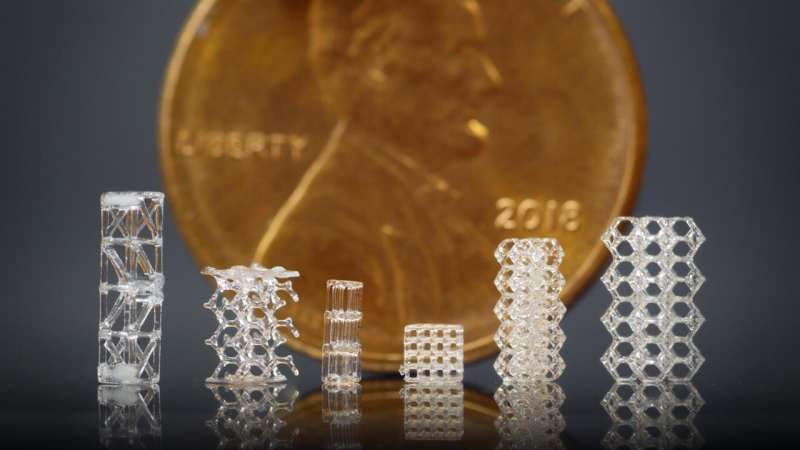
Scientists at UC Berkeley have formulated a new way to 3D-print glass microstructures that is more rapidly and generates objects with higher optical good quality, design flexibility and toughness, according to a new analyze published in the April 15 issue of Science.
Doing work with researchers from the Albert Ludwig College of Freiburg, Germany, the researchers expanded the capabilities of a 3D-printing process they created three yrs ago—computed axial lithography (CAL)—to print a great deal finer functions and to print in glass. They dubbed this new process “micro-CAL.”
Glass is the most popular materials for producing advanced microscopic objects, such as lenses in compact, significant-excellent cameras employed in smartphones and endoscopes, as effectively as microfluidic devices used to evaluate or course of action moment amounts of liquid. But current producing strategies can be gradual, high priced and limited in their skill to meet industry’s expanding demands.
The CAL process is fundamentally various from present day industrial 3D-printing production processes, which build up objects from slim layers of materials. This technique can be time-intense and final result in tough surface texture. CAL, however, 3D-prints the overall object simultaneously. Researchers use a laser to job styles of light into a rotating volume of mild-delicate materials, constructing up a 3D mild dose that then solidifies in the preferred shape. The layer-fewer nature of the CAL course of action enables clean surfaces and sophisticated geometries.
This research pushes the boundaries of CAL to demonstrate its ability to print microscale capabilities in glass structures. “When we very first posted this approach in 2019, CAL could print objects into polymers with options down to about a 3rd of a millimeter in size,” explained Hayden Taylor, principal investigator and professor of mechanical engineering at UC Berkeley. “Now, with micro-CAL, we can print objects in polymers with features down to about 20 millionths of a meter, or about a quarter of a human hair’s breadth. And for the very first time, we have shown how this method can print not only into polymers but also into glass, with capabilities down to about 50 millionths of a meter.”
To print the glass, Taylor and his analysis team collaborated with experts from the Albert Ludwig University of Freiburg, who have made a specific resin material that contains nanoparticles of glass surrounded by a light-weight-sensitive binder liquid. Electronic light projections from the printer solidify the binder, then the researchers heat the printed item to take away the binder and fuse the particles with each other into a sound object of pure glass.
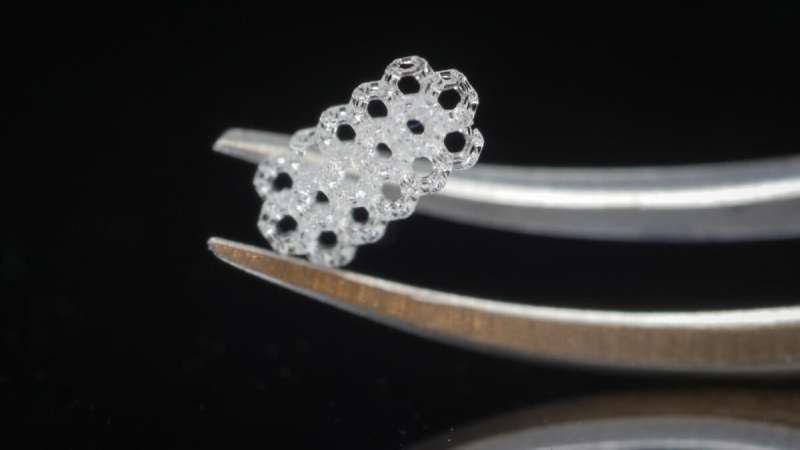
“The essential enabler below is that the binder has a refractive index that is just about similar to that of the glass, so that gentle passes via the content with practically no scattering,” said Taylor. “The CAL printing procedure and this Glassomer [GmbH]-produced substance are a fantastic match for each other.”
The analysis workforce, which bundled guide creator Joseph Toombs, a Ph.D. student in Taylor’s lab, also ran exams and uncovered that the CAL-printed glass objects experienced far more consistent energy than all those made using a common layer-based printing process. “Glass objects have a tendency to split additional conveniently when they incorporate a lot more flaws or cracks, or have a tough floor,” mentioned Taylor. “CAL’s capacity to make objects with smoother surfaces than other, layer-dependent 3D-printing procedures is for that reason a large probable edge.”
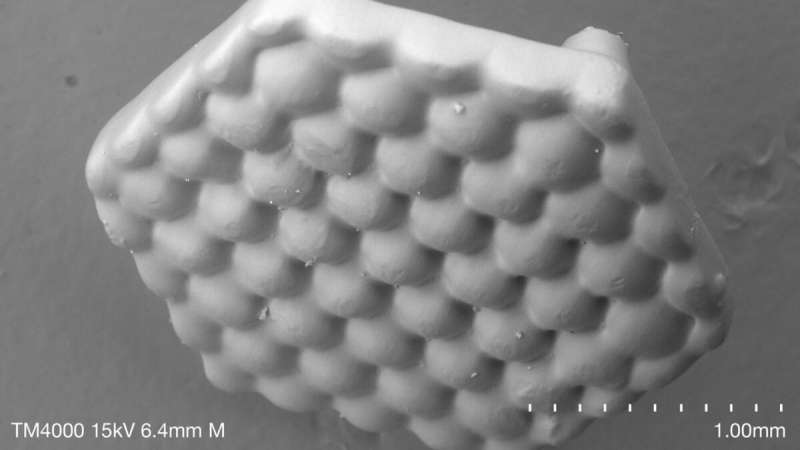
The CAL 3D-printing system delivers companies of microscopic glass objects a new and extra successful way to fulfill customers’ demanding needs for geometry, dimension and optical and mechanical attributes. Precisely, this contains suppliers of microscopic optical components, which are a critical aspect of compact cameras, digital truth headsets, superior microscopes and other scientific instruments. “Being ready to make these factors faster and with a lot more geometric independence could probably lead to new product functions or lessen-price tag goods,” stated Taylor.
Joseph T. Toombs et al, Volumetric additive production of silica glass with microscale computed axial lithography, Science (2022). DOI: 10.1126/science.abm6459
Citation:
New technological innovation 3D prints glass microstructures with rays of gentle (2022, April 15)
retrieved 17 April 2022
from https://techxplore.com/news/2022-04-know-how-3d-glass-microstructures-rays.html
This document is issue to copyright. Aside from any reasonable working for the objective of non-public review or research, no
aspect could be reproduced devoid of the composed permission. The information is provided for info functions only.